

Coupling CO2 and Epoxides
As a downside of the industrial development, carbon dioxide (CO2) concentration in the atmosphere has reached the worrying value of 412.5ppm in 2020 and it is expected to rise further [1]. CO2 is well-known to be a greenhouse gas and, therefore, it is strictly related to global warming and increased water acidity [2,3]. However, thanks to its abundancy, non-toxicity and low-cost, designing carbon neutral processes to convert CO2 into cutting-edge materials represents an appealing challenge.
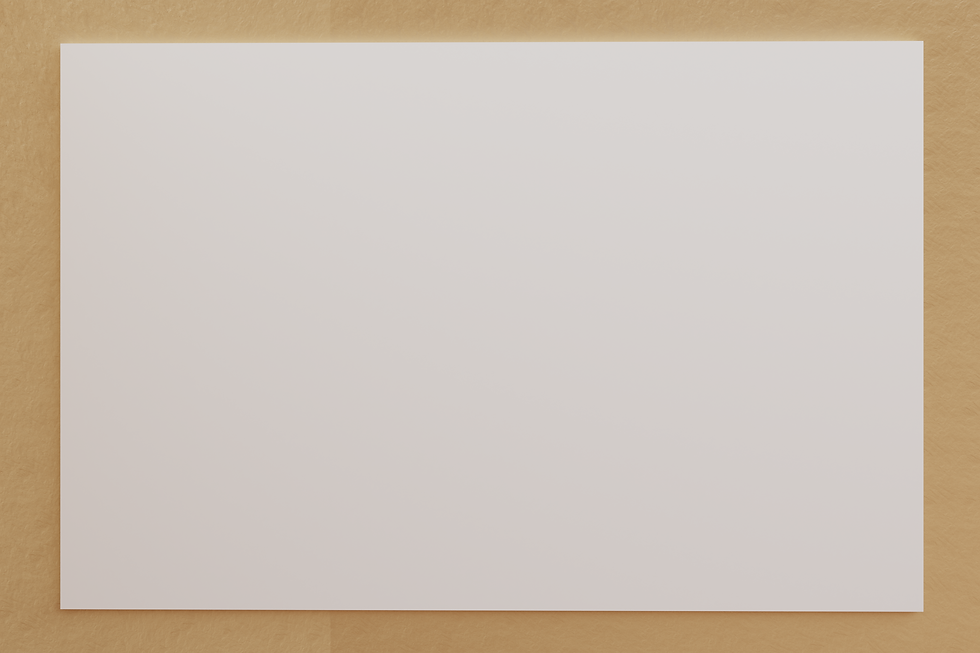
On the right you see the reaction mechanism of the catalytic cycle.
To efficiently catalyse the reaction towards the synthesis of one of the possible products, it is important to finely design the catalytic system and its operating conditions. A good balance between the coordination of ligand, the rigidity of the coordination sphere of the ligand, the acidity of the metal centre (the higher the acidity of the metal centre, the strongly the epoxide is bound to the complex and, thus, the more are the chances that the polymerisation occurs), the nucleophilicity of the nucleophile (if not nucleophilic enough it cannot perform the often rate determinant nucleophilic attack at the carbon of the epoxydic ring), its hindrance (if sterically encumbered, it might be difficult to perform the nucleophilic attack at a sterically hindered epoxide) and leaving group ability (a good leaving group will favour the ring closure of the carbonate intermediate to yield the cyclic product, while a poor leaving group will remain on the polymeric chain favouring its propagation and the synthesis of polycarbonates) are all factor that must be taken into account to dictate the selectivity of the process.[4,5,7] Moreover, a beneficial complex:nucleophile ratio must be chosen in relation to the desired product.[4,5,7] Moreover, also the reaction conditions play an important role in dictating the selectivity of the process: high CO2 pressure and moderate temperature (CO2 in its supercritical conditions) would favour the synthesis of PCs (kinetic product), while higher temperatures and lower pressures are ideal to yield CCs (thermodynamic product).[4]
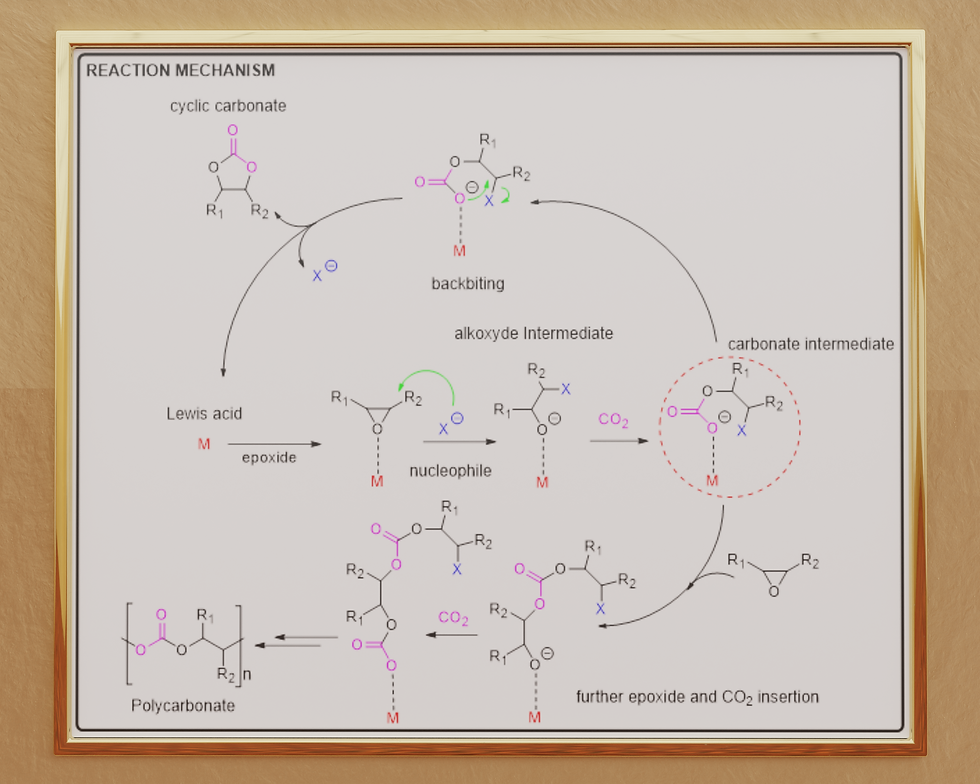
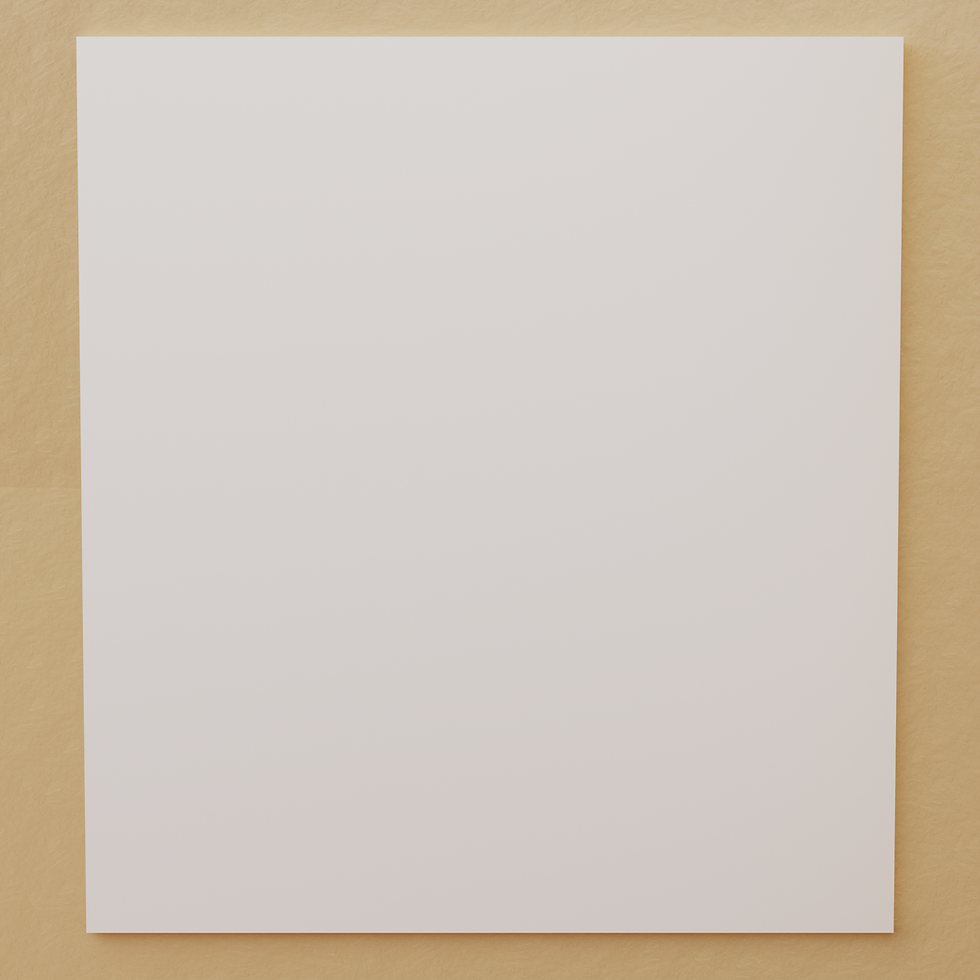
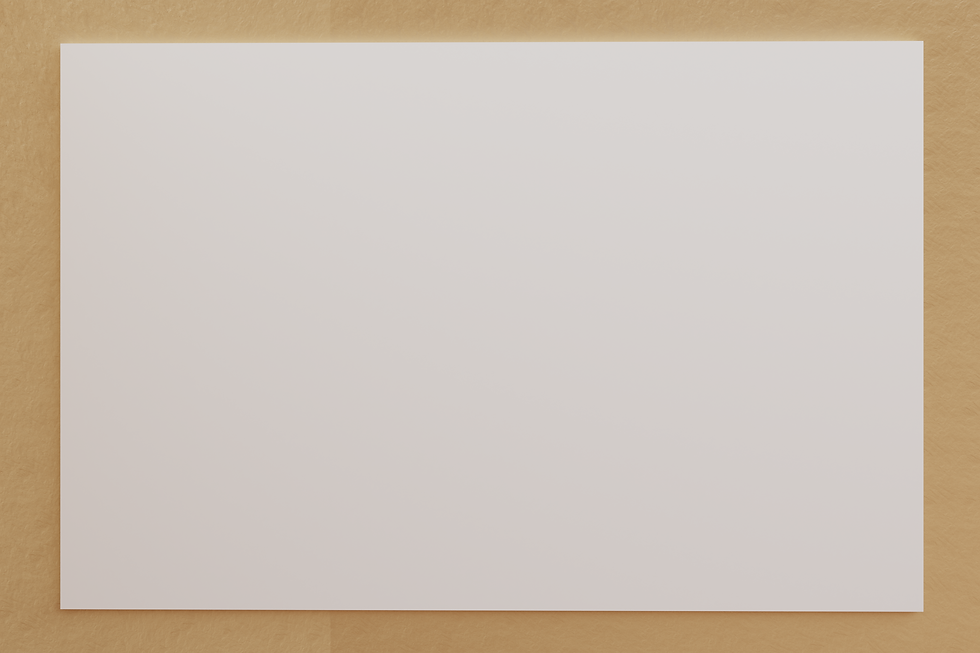
Due to its high thermodynamic stability, CO2 needs to be coupled with high free energy partners (such as heterocyclic compounds, compounds with heteroatoms etc.) to react. In this optic, the atom efficient coupling reaction between CO2 and epoxides is an excellent example of CO2 fixation into value added products [4]. This process can lead to the synthesis of three different products: cyclic carbonates (CCs), which are the thermodynamically favoured product of the reaction and polycarbonates (PCs), which are the kinetic product of the reaction and that are achieved by alternating insertion of CO2 and epoxides. If two epoxide molecules insert subsequently, ether linkages (ELs) are achieved [5]. In this project, the synthesis of PCs is the target and, therefore, CCs and ELs are to be considered by-products. By choosing the right catalyst and by tuning the operating conditions, it is possible to direct the reaction towards the synthesis of the desired product [5].
Catalyst, mechanism and selectivity control
Since when this reaction was discovered in 1969, many catalytic systems have been designed and investigated for the syntheses of organic carbonates and fine tuning of the catalyst was found to strongly influence the yield and selectivity of the process towards one specific product over the competing ones. These catalytic systems might be either homogeneous or heterogenous, which both present positive and negative aspects [5,6]. For instance, heterogeneous catalysts are easily synthesised, low-cost and stable, however they usually require harsher reaction conditions compared to homogeneous catalysts and display lower selectivity. Zinc glutarate (ZnGa) and double metal cyanide (DMC) catalyst are two possible heterogeneous catalyst for the synthesis of this reaction.[6] On the other hands, homogeneous catalyst can be finely tuned to maximise the selectivity towards the desired product under mild conditions; however, their synthesis usually involves multiple steps and the purification procedure in this case might be challenging. A huge range of organometallic complexes have been designed for the synthesis of PCs, among which cobalt, chromium, iron, aluminium, and zinc complexes are, in general, the most active [5]. together with an organometallic complex, the reaction also needs a nucleophile to occur; this might be already present in the complex (bifunctional catalyst) or added to the reaction mixture as a separate species (binary catalyst). Bulky organic salts are commonly used as nucleophiles. Due to their high selectivity, fine tuning, and milder operating conditions, homogeneous catalysts are usually preferred over heterogeneous catalysts [5,6].
For what concerns the mechanism, in general, the coupling reaction between carbon dioxide and epoxides needs to be catalysed to occur and, depending on the catalytic system, the first step that initiates the reaction might either be the coordination of the epoxide or carbon dioxide [7]. The most common mechanism in the case of homogeneous catalysts is the monometallic mechanism [7], in which the first step is usually the coordination of the epoxide to the metal centre; this activates the epoxide and favours the nucleophile to open the epoxydic ring leading to an alkoxide intermediate. At this point, carbon dioxide inserts between the negatively charged alkoxide intermediate and the metal centre to generate a metal carbonate intermediate. This species is now the key intermediate of the reaction as it can undergo intermolecular backbiting to lead the corresponding CCs or it can allow further epoxide and CO2 insertions to yield the desired PCs [7].


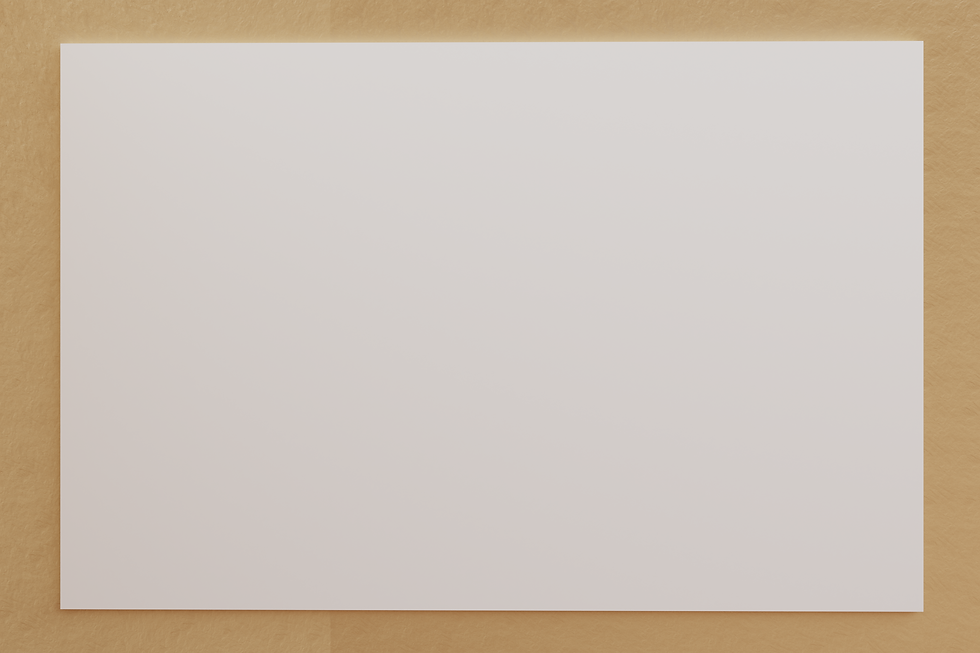
CO2 as reactant for the synthesis of PCs
The set-up to perform the copolymerisation between CO2 and epoxides to PCs in supercritical conditions consists of a high-throughput CO2 reactor unit manifactured by ILS-Integrated Lab Solutions GmbH. This CO2 reactor unit consisted of: (a) a 10-reactors block, which allows 10 experiments to be performed simultaneously in individually stirred batch reactors (84 mL volume each, 30 mm internal diameter); and (b) a single, batch reactor of the same size supplied with a borosilicate glass window to allow visualization of the phase behavior within the reactor.
On the right you see a picture of the reactor setup.
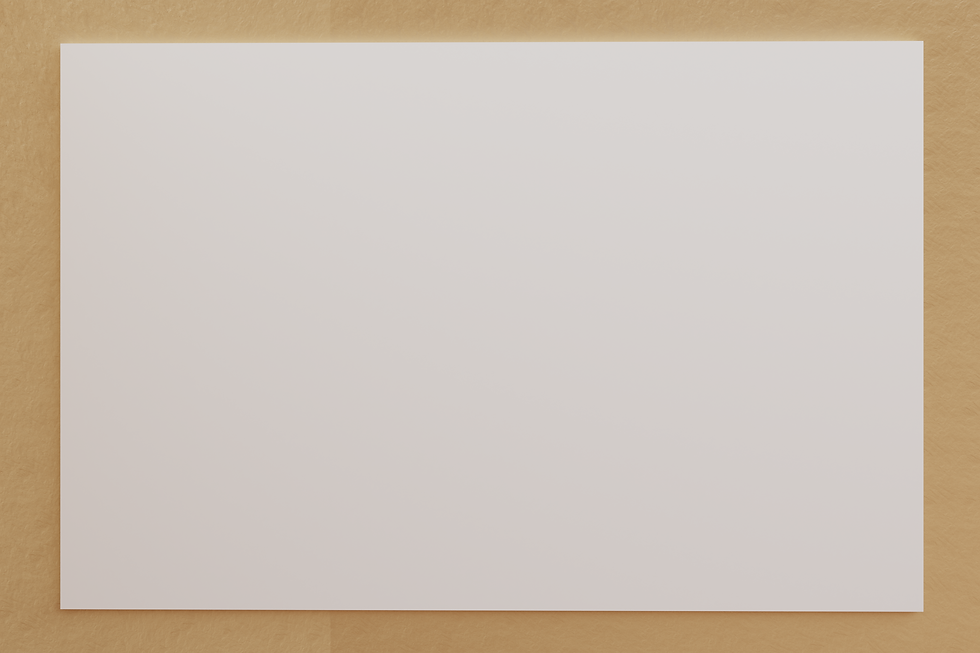
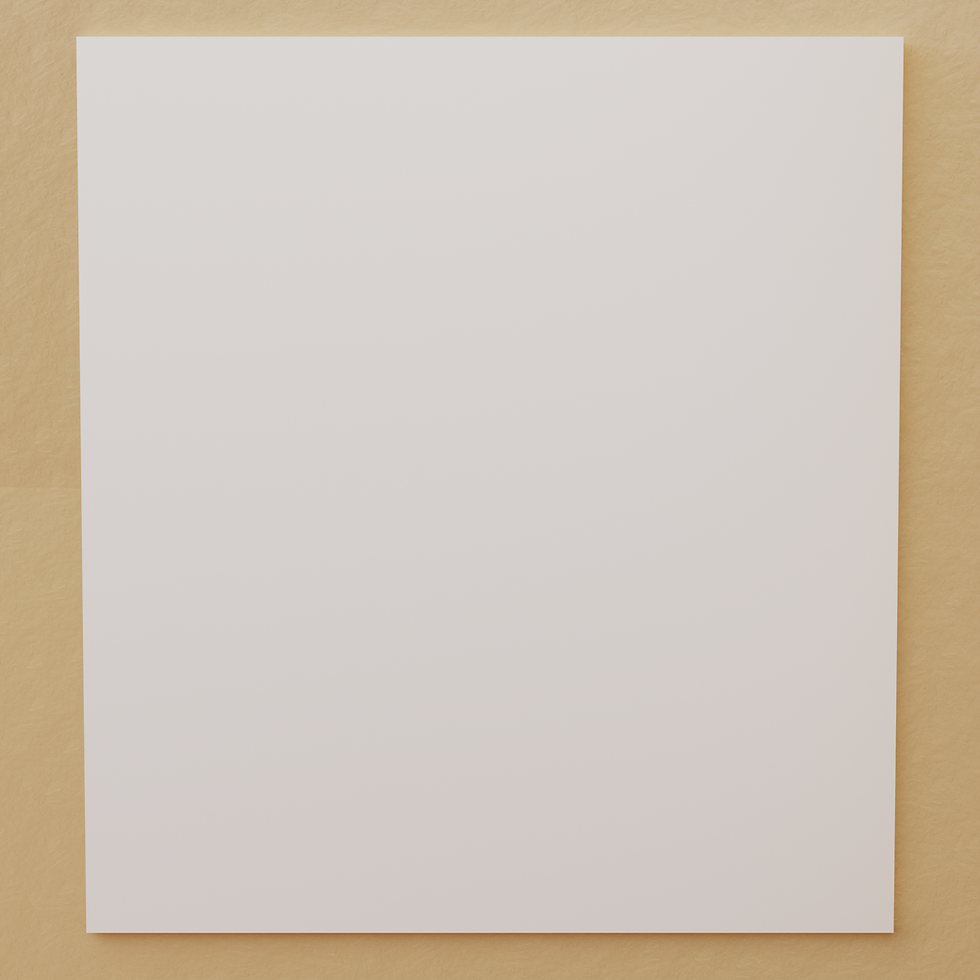
Increasing the sustainability of the reaction
With the increase of the awareness of the depletion of crude oil derivatives and the growing concerns relative to the impact that industrial processes might have on the environment, many chemical companies are putting efforts in the development of cutting-edge materials that are derived from biomass and renewable feedstocks but that also display properties that are comparable to those of commercially available synthetic products. Moreover, due to the impact that the CO2 has on the environment as the first contributor to the greenhouse effect, its conversion into valuable materials is even more desirable.
Even though the coupling reaction between carbon dioxide and epoxides was discovered in 1960, it was only in the last decades that, with the development of highly active and selective catalysts, this synthetic route to polycarbonates started to be intensively studied and exploited. However, up to date this reaction has been mainly investigated for crude oil-based epoxydic substrates (such as propylene oxide and cyclohexene oxide) and most of the catalytic systems employed to catalyse the process is based on heavy metals, which also have a polluting effect on the environment.[4-8] For these reasons, to further increase the sustainability of this synthetic process, only (entirely or partially) bio-based epoxides will be coupled with CO2 to produce polycarbonates (and cyclic carbonates, the competing by-product) in agreement with the 12 Principles of Green Chemistry we have on display in the atrium. Furthermore, only earth-abundant metal-based catalysts will be employed during this study (as they are nontoxic and cost-effective) to minimise the environmental impact of the reaction.
References
[1] R. Lindsay, Climate Change: Atmospheric Carbon Dioxide 2020. Published online at Climate.gov. Retrieved from http://climate.gov
[2] P. N. Pearson, M. R. Palmer, Nature 2000, 406, 695-699
[3] H. Ritchie, M. Roser, CO₂ and Greenhouse Gas Emissions 2017. Published online at OurWorldInData.org. Retrieved from: https://ourworldindata.org/co2-and-other-greenhouse-gas-emissions.
[4] M. Taherimehr, P. P. Pescarmona, Journal of Applied Polymers Science 2014, 131, 21
[5] A. J. Kamphuis, F. Picchioni, P. P. Pescarmona, Green Chemistry 2019, 21(3), 406-448
[6] Kember, M. R., Buchard, A., Williams, C. K. (2011). Catalysts for CO2/epoxide copolymerisation. Chemical Communications, 47(1), 141-163
[7] P. P. Pescarmona, M. Taherimehr, Catalysis Science &Technology 2012, 2(11), 2169-2187
[8] Poland, S. J., Darensbourg, D. J. (2017). A quest for polycarbonates provided via sustainable epoxide/CO2 copolymerization processes. Green Chemistry, 19(21), 4990-5011