
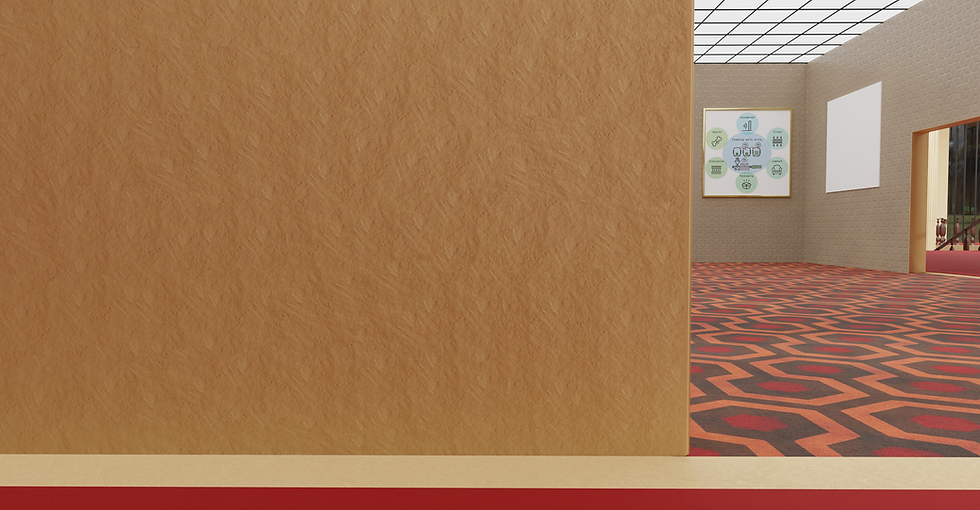
Biodegradable Foams
Polymeric foams, or plastic foams, have several characteristics that make them very attractive for different markets. Due to their versatility, nearly all consumer product industries produce or utilize some type of polymer foams. The wide-ranging market for foams includes home appliances, food industries, spacecraft, etc. However, due to its notable features, it is used extensively, wrong discarded in large quantities and sometimes produced by chemical reaction leaving pollutants over the process. Therefore, it is important that most of the polymer foam should be replaced by a biodegradable material with a sustainable production. One of the possibilities to tackle the environmental process issue is to utilize supercritical carbon dioxide (scCO2) since it is a ‘green’ solvent, thus facilitating a sustainable method of producing polymer foams. ScCO2 is non-toxic, chemically inert, and compatible with nearly all polymers.
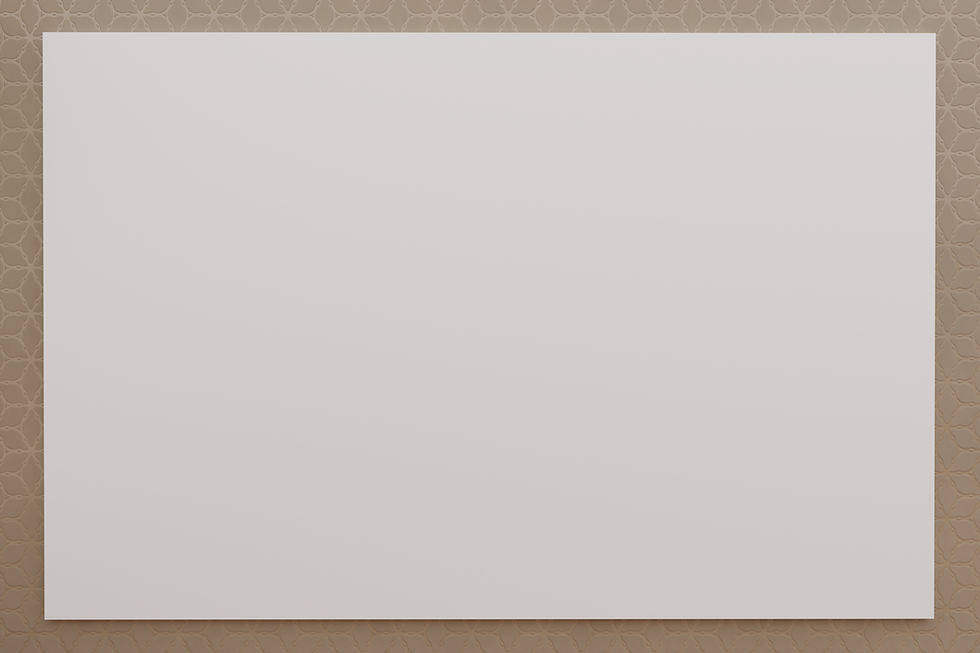
The foam process, involves a lot of different parameters, therefore it is important to understand how each polymer behaves not only at normal conditions, but also embedded in scCO2. For that we are utilizing different techniques to characterize a set of biodegradable polymers and evaluating how it will influence the foaming and final mechanical properties. After the chemical characterization, it is important to access the mechanical properties of the polymer melt, so we can decide what range of temperature might be suitable in order to foam the biodegradable foam. If temperature is too low and the polymer is not completely melted, there will be no expansion. However, if too hot, the polymer might foam uncontrollably, and most likely after the expansion, the cells will collapse because the polymer still behaves as a liquid other than a solid to maintain its shape. To understand how the cells will be formed and if the cells will merge at certain point, it is also interesting to understand how the polymer stretch at temperatures near the melt point, where most of the action will take place. In addition to the described mechanical properties, it is relevant to measure everything again, but under scCO2 environment and how much CO2 each polymer can absorb under a range of temperatures and pressures. Unfortunately, mechanical properties under scCO2 is not always possible due to equipment limitations, but there are enough theories and techniques to overcome such problems.
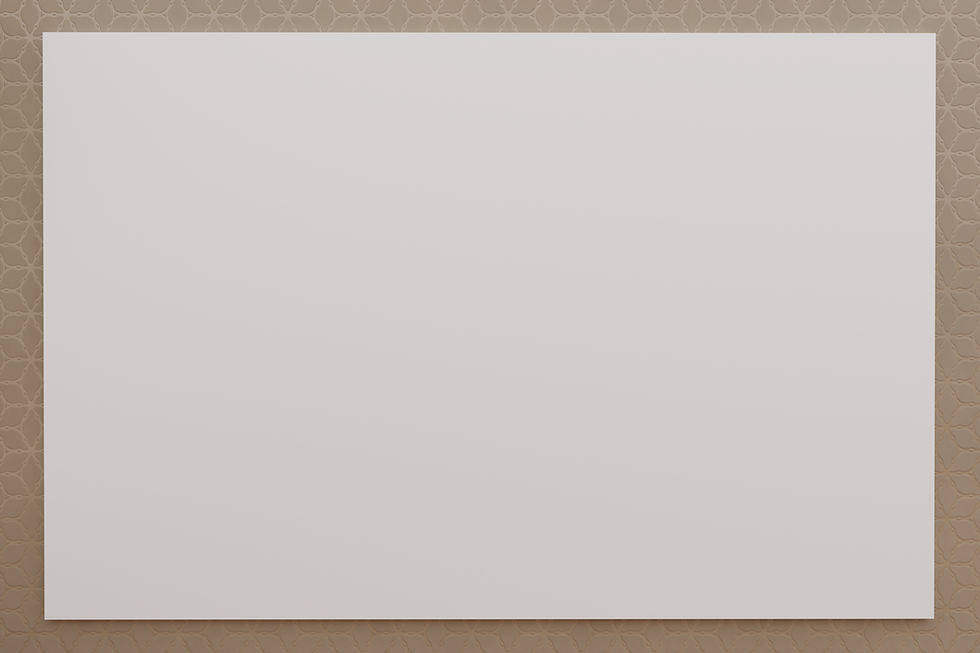

Secondary influences can also be added to the procedure to make the “perfect” biodegradable foam. Using a co-blowing agent during the production may improve the foaming performance of the foam. Usually co-blowing agents are solvents as ethanol and can enhance the solubility of CO2 increasing the cell size and possibly enlarge the process temperature window. More product possibilities can be achieved by playing with the formulation of the polymer before foaming. Additive, fillers and chemical modifications will add features to the matrix that will reflect in the polymer foam. Additives, mostly improve the process, making possible to foam easily polymers that for instance have low solubility. Fillers have two important roles, first it change mechanical properties of the polymer as expected in any polymer material. In addition, fillers play a second, as important as, task of being the nucleation site during the foaming process, meaning that the CO2 before the foaming, will be trapped with the filler assisting in the homogeneity and cell size during the foaming, therefore having a more controlled of the foam structure [7]. Modifying polymers with branching agents or using polymers with different molecular weights tend to produce different outcomes in the same process. Branching agents are a good example of simple modification, being able to enhanced viscosity, shear sensitivity and longer relaxation time.
On the right you see foam structure of specific biodegradable polymer foamed at different temperatures and pressures.
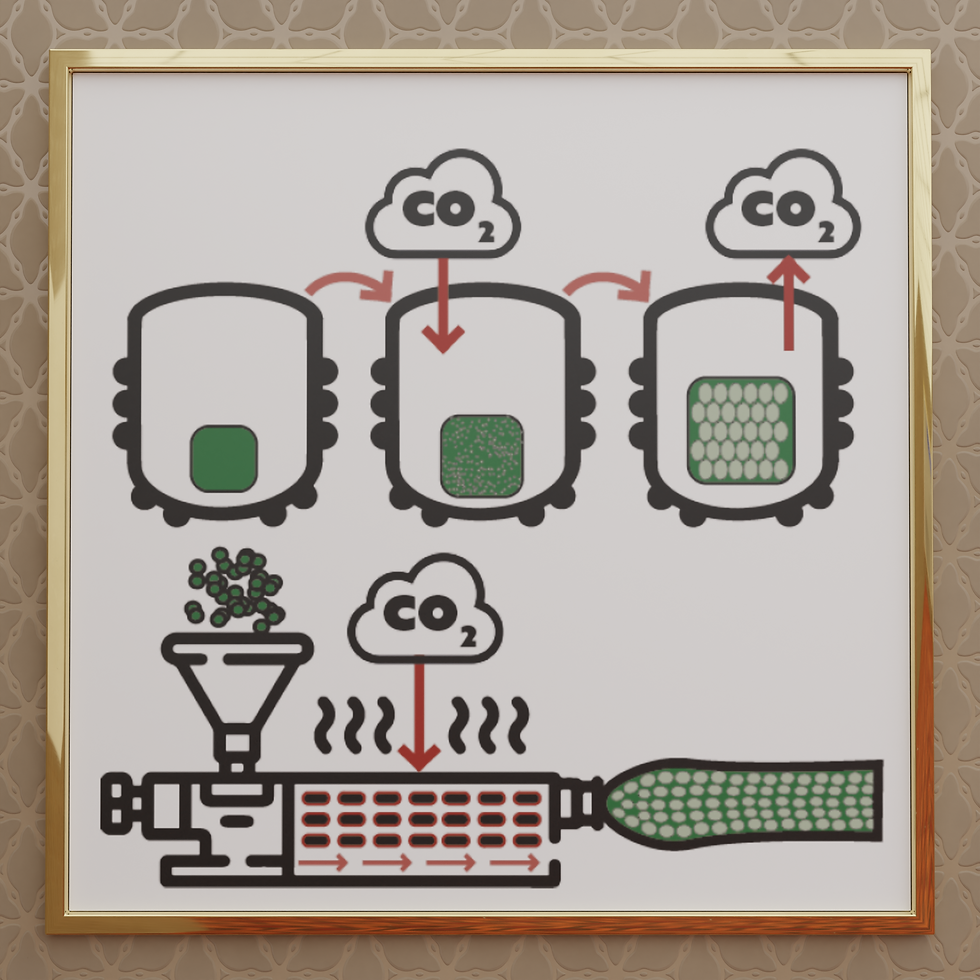
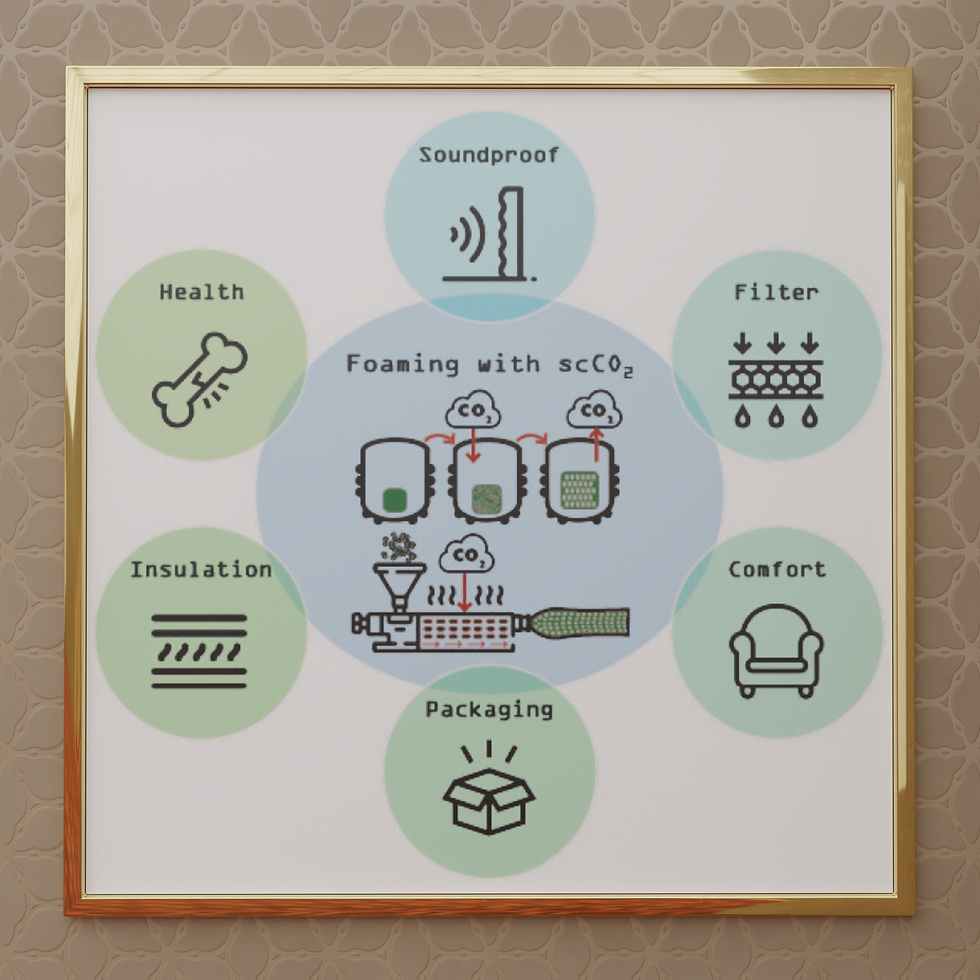
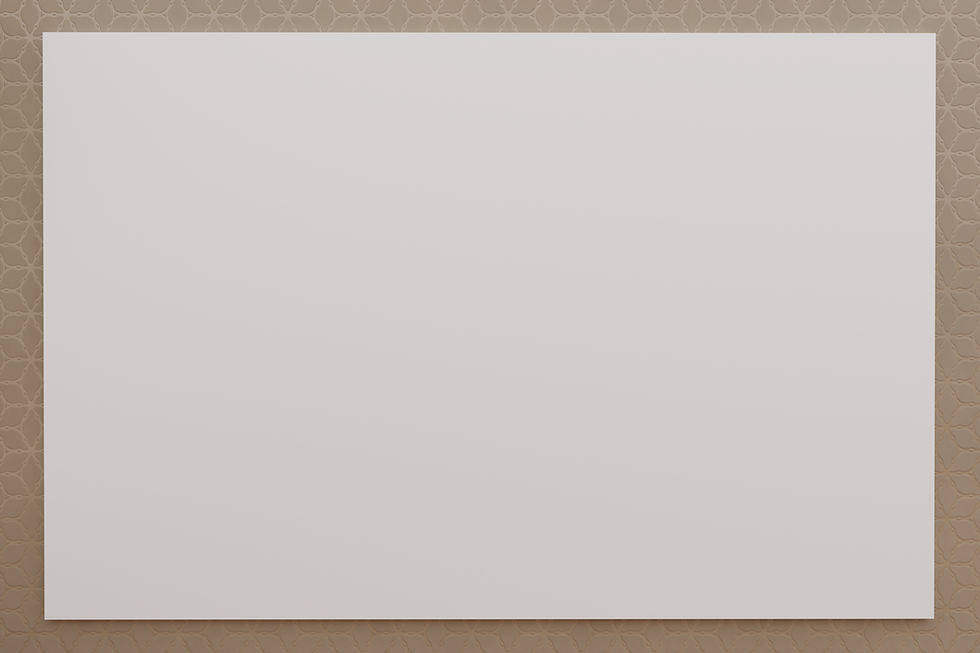
Foams attractive tuneable features are gained from the porous structure, and create products with impressive compressibility, thermal insulation, lower density, impact absorption, structure reinforcement, filter, etc. To manufacture a polymeric foam, blowing agents are necessary to produce a cellular structure in the matrix of the polymer. Essentially, there are two types of blowing agents used to produce polymeric foams; physical and chemical blowing agents. Most of the chemical blowing agents are solids at standard conditions (STP) for temperature and pressure that undergo a chemical reaction releasing gas [1]. Physical blowing agents are in general liquid or gas under STP that are subjected to a change of state and expansion to form pockets within the polymer matrix [2]. In general, chemical blowing agents, come with problems related to product contamination, problems with foam recycling and usually not environmental friendly.
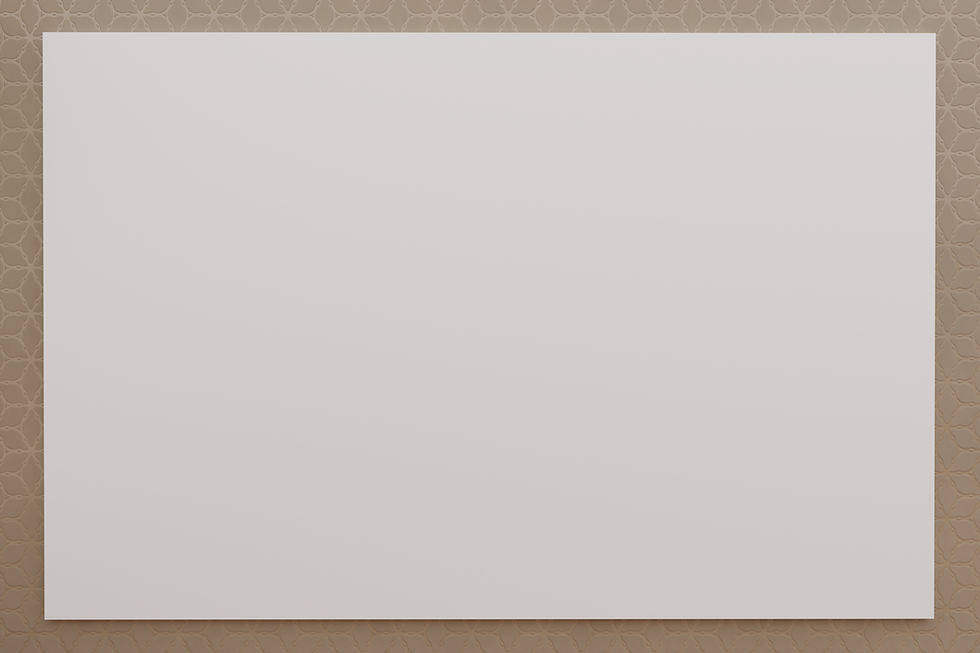
Steps to better understand the process
At the moment we could identify at least three potential biodegradable polymers for foaming in which there are potential market, within one of them being biobased. In the future we intend to foam with the optimal conditions according to our findings in the characterization step, and measure mechanical properties and any relevant feature after foaming. With that we will prove that biodegradable polymers can be processed with a environmental friendly way and are suitable to substitute some of the polymer foams utilized in the market in the present-day
On the right you see three types of rheometers: (A) Parallel plate (B) Extensional (C) Rotational with Pressure-cell
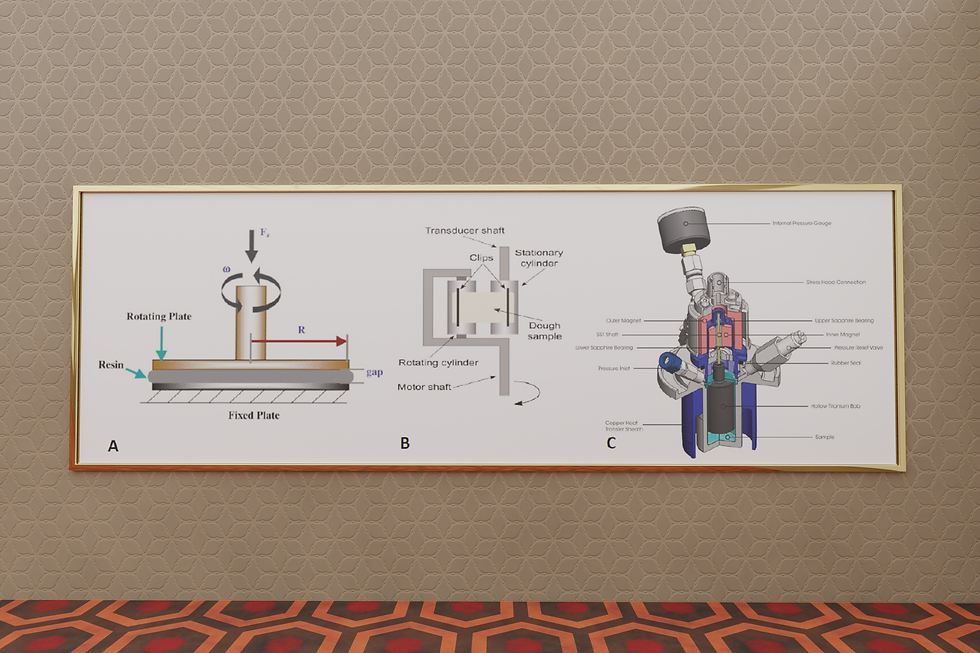
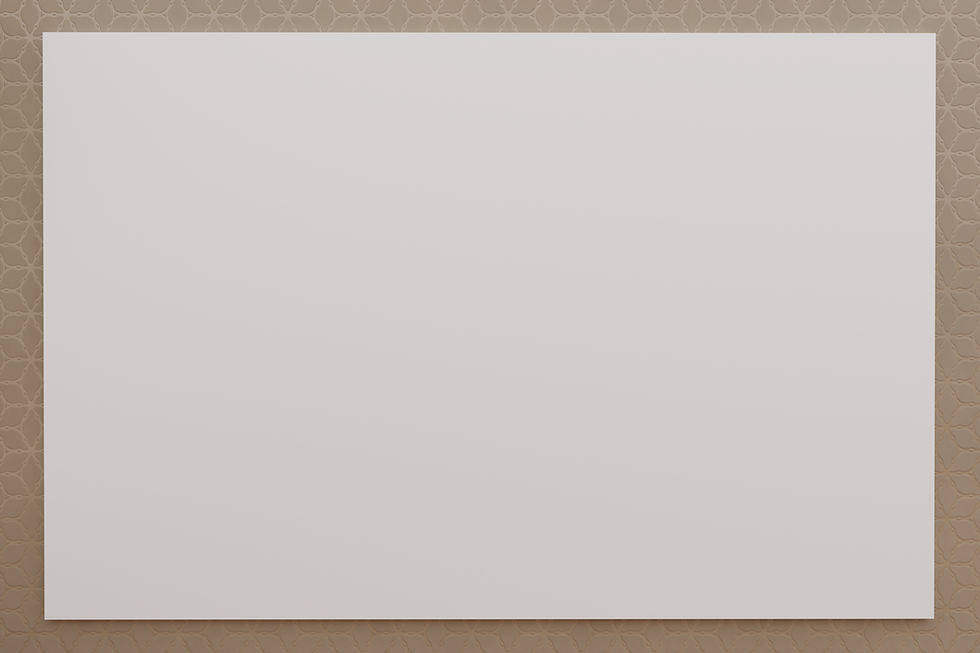
In contrast, physical blowing agents as CO2 is a ‘green’ solvent, thus facilitating a sustainable method of producing polymer foams. CO2 is minimally toxic, chemically inert and in its supercritical state it is soluble in molten plastic. Supercritical CO2 can act as a plasticizer, decreasing the viscosity of polymers, facilitating the foaming process.The process of producing foams in most of the cases uses batch or extrusion, and in both cases, scCO2 can be utilizes since foaming rely on the mechanism of nucleation, growth and expansion. Utilizing supercritical fluids in the process of polymer foaming offers many benefits. Fluids in supercritical conditions combine the viscosity of gas and the density of a liquid, therefore performing as an excellent solvent, plasticizer and enhancing the expansion of the polymer [3].
Polymer foaming process assisted with scCO2 has many advantages, nonetheless utilizing scCO2 in the foaming has many variables and parameters to be tuned, independently of the process. Operational temperature and pressure directly influence the density of the scCO2, thus making the supercritical fluid behave more or less like a gas or liquid [4]. The density of the scCO2, therefore has a direct impact in reaction with the polymer, resulting in different outcomes concerning morphology and mechanical properties. Moreover, the polymer itself will change its behaviour according to the environment that is being treated or formulation if the case [5].
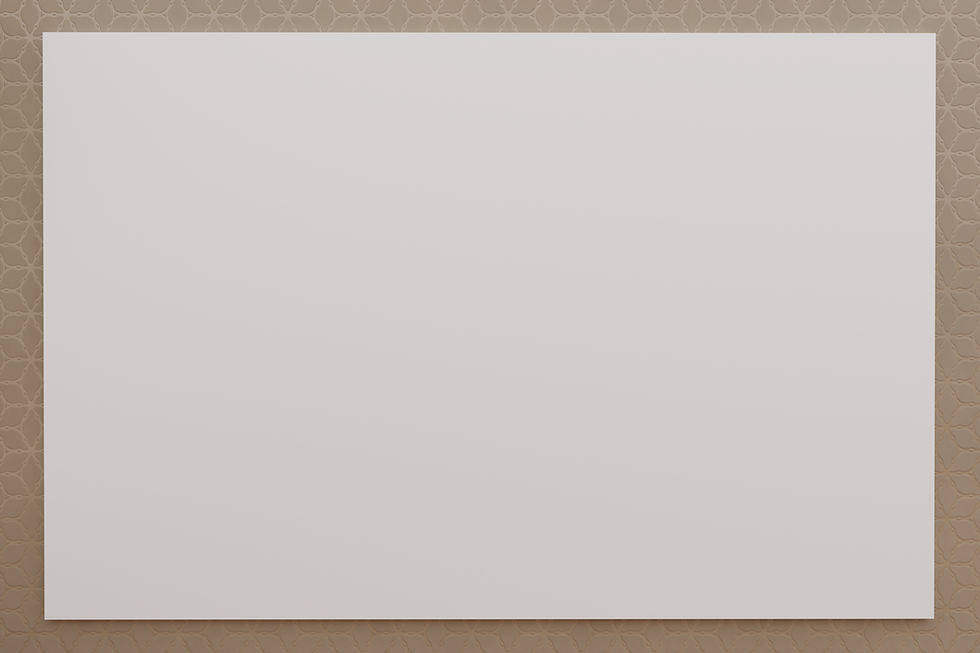
Current progress with scCO2 polymer foaming
As mentioned, many parameters will influence the production of biodegradable foams, but as unwritten rule, the pressure is more relevant for the foam uniformity than the polymer residence time. Foaming time or depressurization rate is directly related and proportional to the foam density, and consequently, inversely proportional to the overall porosity. Adjusting the concentration of scCO2 load during the process can be challenging since it might influence the plasticizing effect of the polymer. In other words, the higher the concentration of scCO2, the less energy will be necessary to reach the point where the rigidity of the polymer drops. Therefore, in some cases, increasing the concentration of scCO2 might result in the need to adjust other parameters such as temperature and pressure to counterbalance the polymer plasticization [6].
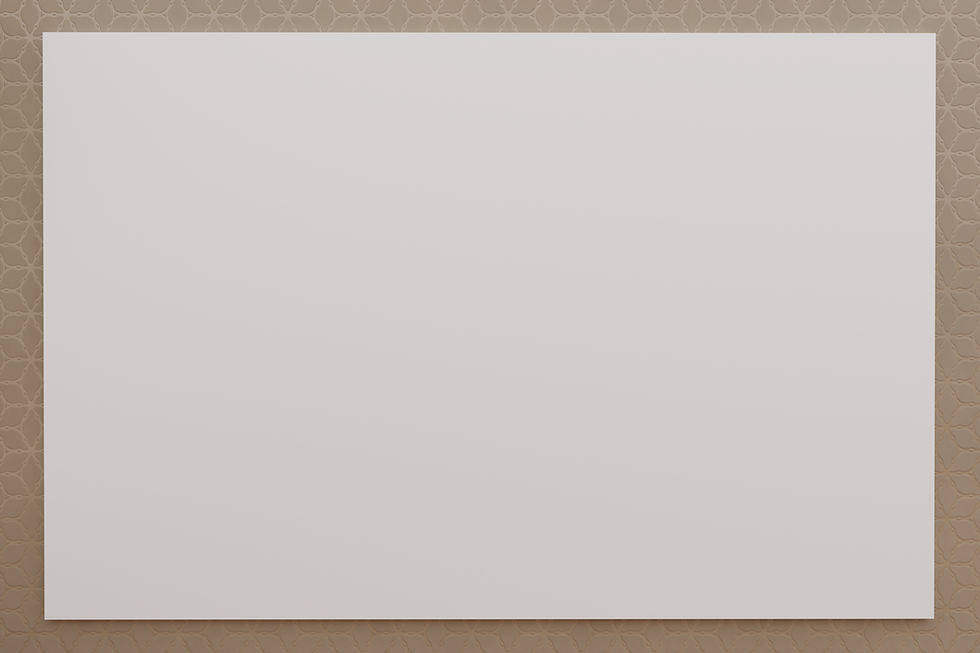

[1] Rohleder, M.; Jakob, F. In Specialized Injection Molding Techniques; Heim, H.-P., Ed.; William Andrew Publishing, 2016; pp 53 – 106.
[2] Yonezu, A.; Hirayama, K.; Kishida, H.; Chen, X. Characterization of the compressive deformation behavior with strain rate effect of low-density polymeric foams. Polymer Testing 2016, 50, 1–8.
[3] Watanabe, M.; Hashimoto, Y.; Kimura, T.; Kishida, A. Characterization of Engineering Plastics Plasticized Using Supercritical CO2. Polymers 2020, 12, 134.
[4] Ngo, M. T.; Dickmann, J. S.; Hassler, J. C.; Kiran, E. A new experimental system for combinatorial exploration of foaming of polymers in carbon dioxide: The gradient foaming of PMMA. Journal of Supercritical Fluids 2016, 109, 1–19.
[5] Mills, N. Polymer foams handbook: engineering and biomechanics applications and design guide; Elsevier, 2007.
[6] Zhou, C.; Wang, P.; Li, W. Fabrication of functionally graded porous polymer via supercritical CO 2 foaming. Composites Part B: Engineering 2011, 42, 318–325.
[7] Liu, P.; Chen, W.; Jia, Y.; Bai, S.; Wang, Q. Fabrication of poly (vinyl alcohol)/ graphene nanocomposite foam based on solid state shearing milling and supercritical fluid technology. Materials and Design 2017, 134, 121–131.