
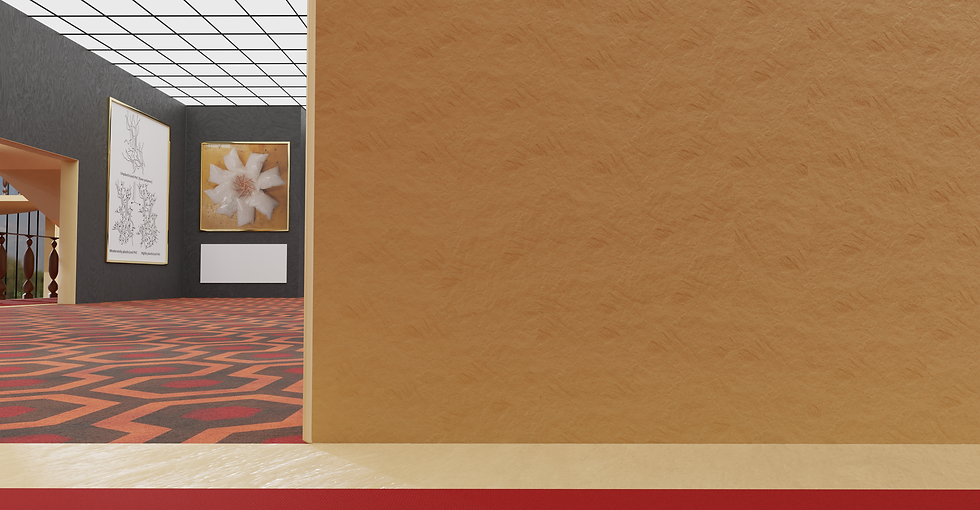
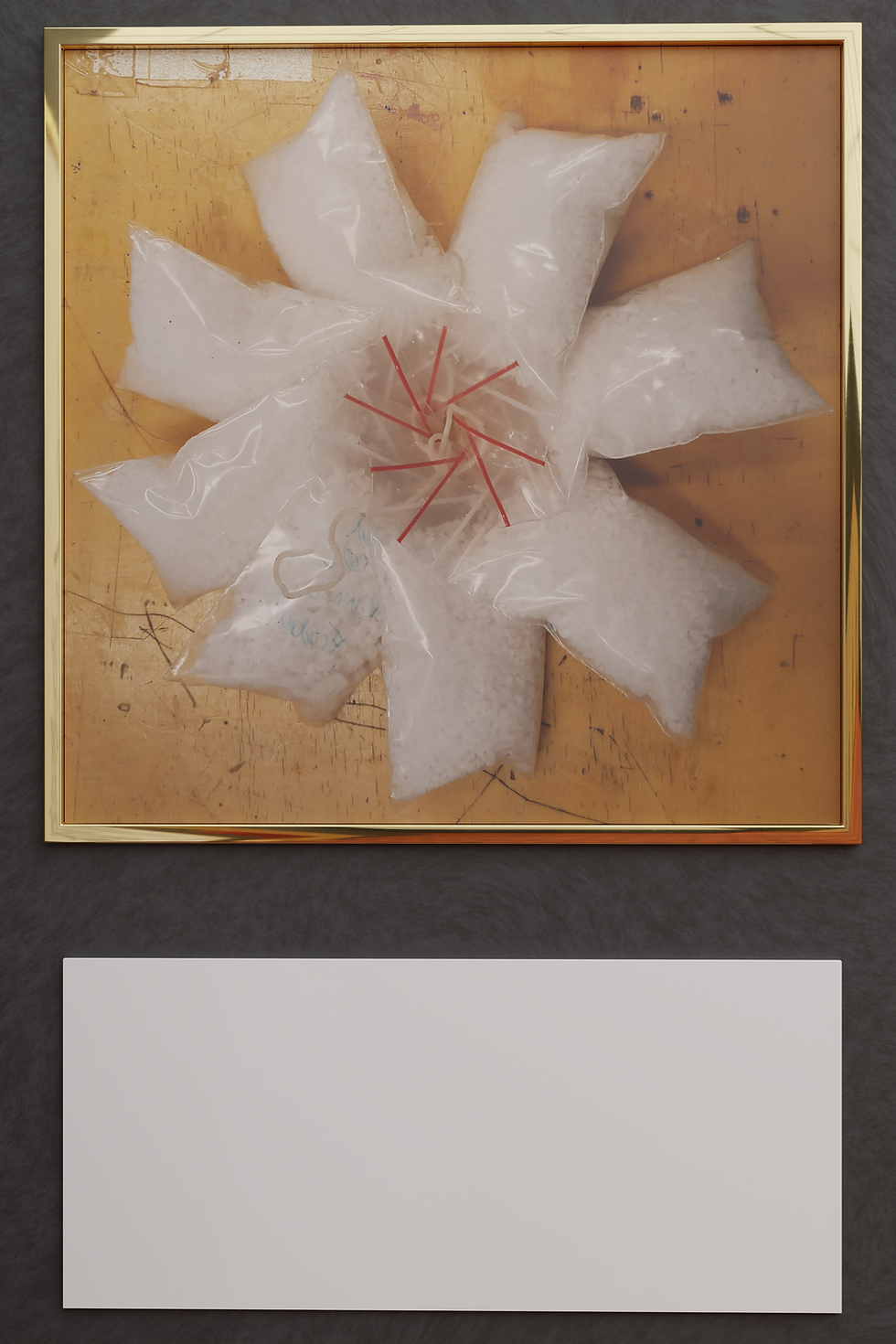
Recycling and Reusing of Plastics
Nowadays, environmental and human safety concerns are noteworthy factors while developing chemical processes. In conventional polymer processing, environmentally hazardous volatile organic compounds (VOCs) are used, either as a reaction medium as a processing medium for shaping, extraction, impregnation, or viscosity reduction [1]. Considering the total global production of plastic is roughly 360 million tons (in 2018) and because the whole polymer processing is related to toxicity and non-biodegradability, companies are investigating options for more sustainable processes [2]. One of the promising techniques to obtain a more sustainable and non-toxic process is the use of supercritical fluids.
The aim of the present work is to review more recent developments in the field by outlining the current and future challenges from a scientific and technological point of view. The focus will be on extraction methods with the use of supercritical carbon dioxide (scCO2) and upgrading of used plastic with scCO2 reactive extrusion.
The aim of the present work is to review more recent developments in the field by outlining the current and future challenges from a scientific and technological point of view. The focus will be on extraction methods with the use of supercritical carbon dioxide (scCO2) and upgrading of used plastic with scCO2 reactive extrusion.


References
[1] Nalawade, SP., Picchioni, F., Janssen, LPBM. & Nalawade, S. P., Supercritical carbon dioxide as a green solvent for processing polymer melts: Processing aspects and applications, 2006, In : Progress in Polymer Science. 31, 1, p. 19-43
[2] PlasticEurope. Plastic—The Fact 2017: An Analysis of European Plastics Production, Demand and Waste Data; Plastic Europe: Brussels, Belgium, 2018
[3] R.N. Cavalcanti, M.A.A. Meireles, 2.07 - Fundamentals of Supercritical Fluid Extraction, Comprehensive Sampling and Sample Preparation, Analytical techniques for scientists, Volume 2, 2012, Pages 117-133.
[4] Iqbal, M., Mensen, C., Qian, X. and Picchioni, F., Green Processes for Green Products: The Use of Supercritical CO2 as Green Solvent for Compatibilized Polymer Blends, Polymers 2018, 10, 1285.
[5] Ramos-Devalle, L. F. (1988) Plasticization of poly(vinyl chloride): PVC/plasticizer compatibility and its relationship with processing and properties of plasticized PVC. Loughborough University.

Supercritical CO2 extraction
Polyvinyl chloride (PVC) is the third-most widely produced polymer next to polyethylene (PE) and polypropylene (PP). There are two forms of PVC, namely rigid/stiff PVC and soft PVC. To obtain soft PVC, plasticizers are added to the PVC. These plasticizers make the PVC more flexible and they lower the glass transition temperature. The most commonly known plasticizers are phthalates e.g., dioctyl phthalate (DOP), Diisononyl phthalate (DINP). Considering the amount of plastic waste produced every year, one of the options might be to turn soft PVC back into rigid PVC by removing the phthalates. Nevertheless, when talking about recycling of PVC, men only speak of recycling the rigid PVC due to the difficulties of removing phthalates from the PVC matrix.
If one considers a piece of solid plastic containing a plasticized polymer, a fraction of the plasticizer molecules would be located on the direct surface of the piece and the rest would be inside the piece. The plasticizer molecules on the surface can be easily absorbed by the extracting solvent, while the molecules inside the solid piece are more difficult for the solvent to contact. Hence, the distribution of solute molecules in the solid matrix affects the extraction efficiency. In the figure, areas containing ordered strands of polymer are interspersed with areas of disordered strands of polymer. It can be observed that as plasticizer content is increased the total area of disorder is increased along with the free volume of the matrix. The changed structure would allow the solvent to penetrate through the matrix more easily and hence, to extract more solute.
Translating the process described above to the real deal, we are using an extractor as set-u. The scCO2 enters the reactor which is filled with soft PVC. The scCO2 enters the polymer matrix and the phthalates start to dissolve in the scCO2. The saturated scCO2 leaves the reactor while the PVC stays behind. In the separator the scCO2 is turned into a gas and the phthalates can now be separated from the gas stream.
Afterwards we can analyse the PVC in the reactor by IR to check whether all the phthalates have left the matrix. Especially working at high pressure (300-400 bar) extraction efficiencies of 90% were achieved.
On the left you see a picture and a schematic of the extractor setup. A visual representation of the typical solid matrix for plasticized PVC is depicted below that.
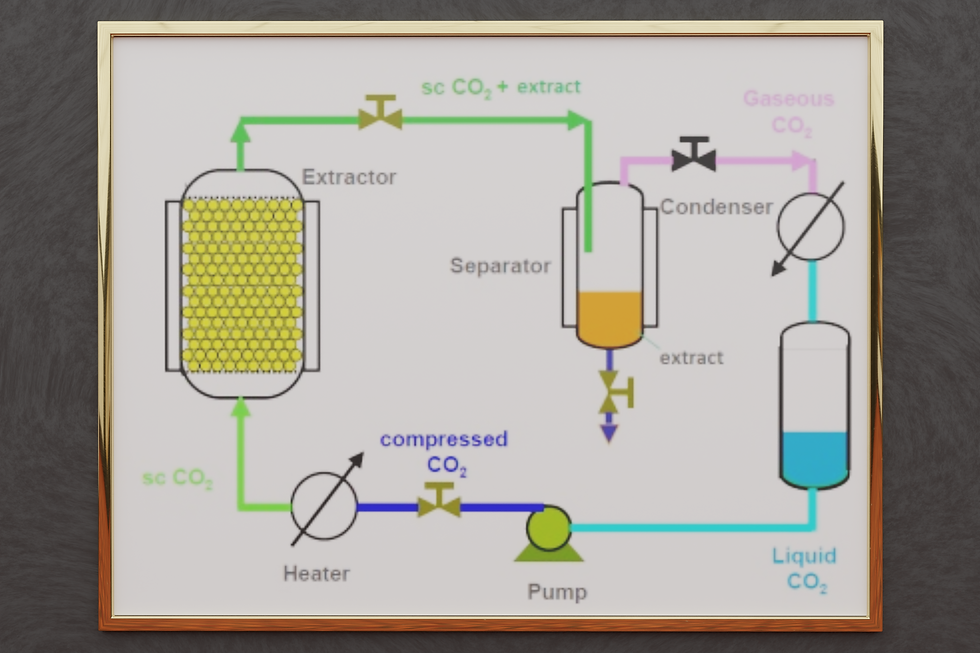


Reactive Extrusion and Blending with scCO2
Polyolefins, especially low-density polyethylene (LDPE), high-density polyethylene (HDPE), and polypropylene (PP), are widely used thermoplastics for multiple industrial and technological applications due to their mechanical properties, ease of processing, versatility and low price. This automatically results in an enormous amount of plastic waste streams in addition to the fact that most plastics are still produced from fossil fuels. Therefore, efficient processes are being developed to limit the disposal of plastic waste. One of these options is material recycling. During this process, the plastic waste is converted into a recycled type of raw material for the production of new materials.
In order to ‘upgrade’ the plastic waste into something useful reactive extrusion or polymer blending can be performed. Polyolefins are grafted with monomers containing reactive groups in order to improve the mechanical properties during reactive extrusion. The other alternative such as polymer blending, a mix of polymers are blended in order to create a new material with different properties.
To improve the grafting of the monomers onto the polymer matrix or the blending of polymers supercritical CO2 can be used. Supercritical CO2 has the advantage of lowering the viscosity of the melt phase that will lead to a lower process temperature and finer dispersion of the used materials. A reduction in interfacial tension of the polymers caused by the addition of scCO2, may also contribute to enhanced polymer blending. Moreover, scCO2 has a plasticizer effect that results in a lower glass transition temperate (Tg) and a more flexible and softer polymer [4]. The plasticizer effect combined with the swelling effect of scCO2 enables not only interactions on the polymer surface, but also into the polymer matrix.
The machine used for these 2 processes is a twin-screw extruder. The extruder consists of 2 screws that just keep rotating. The screws are completely cover by the HZ ‘chambers’ that all have a separate heating element. The chemicals (pre mixed) enter the hopper (H1) and scCO2 is added to the system as well. The two counter-rotating screws will transport the polymer melt along the 5-heating zones to the die. The die pressure is measured by pressure indicator P2 so that we can know the pressure inside the extruder, just before it leaves the system.
Overall, a higher grafting degree, less crosslinking, and lower process temperatures are expected when grafting and blending under scCO2 conditions compared to the traditional melt grafting/blending.
On the left you see a picture and a schematic of the extruder setup.

