

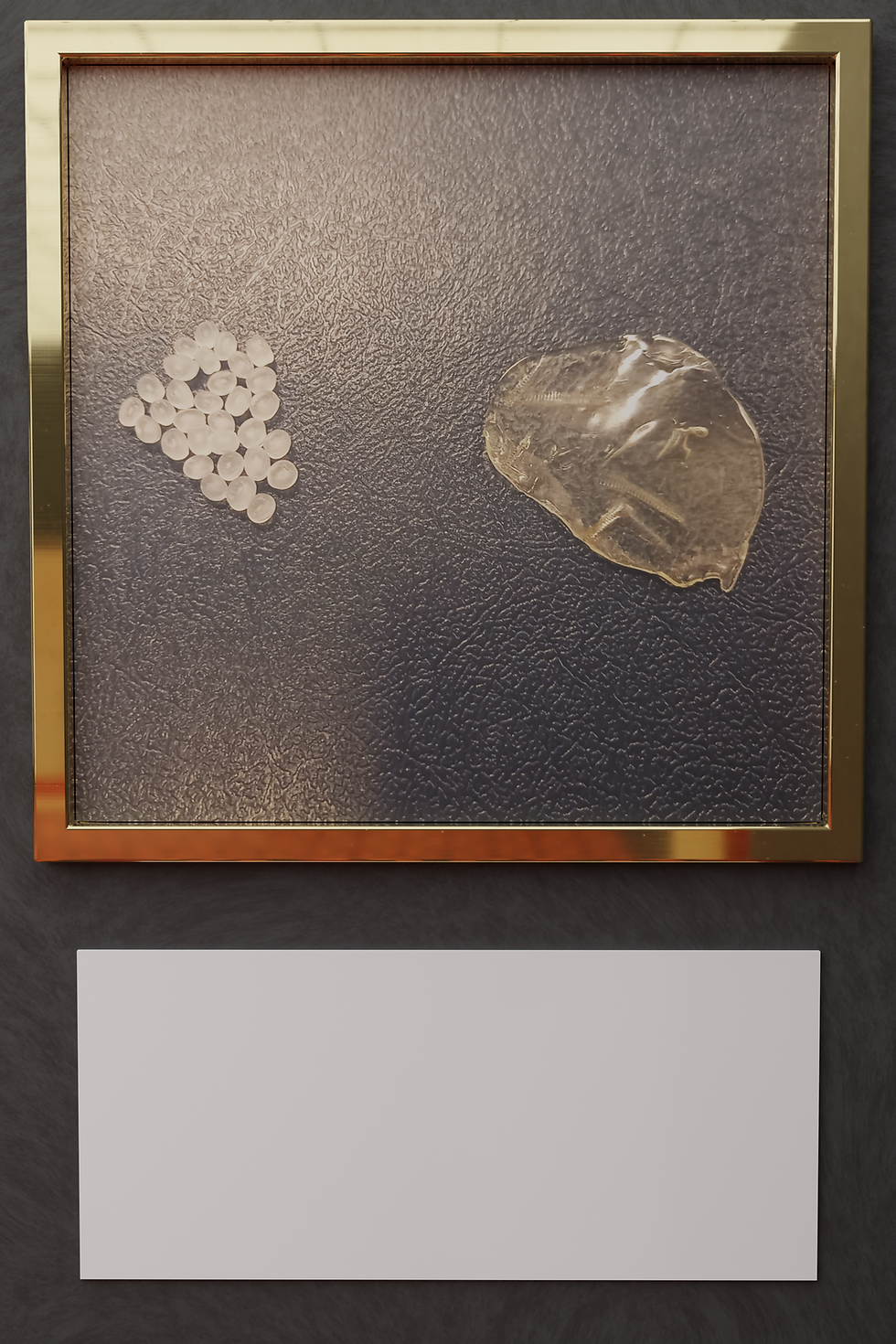
Disturbing Regularity
in Polypropylene
For a long time, atactic polypropylene (APP) was made as a by-product of isotactic polypropylene (IPP). APP has applications in adhesives, waterproof materials, but predominantly in the bitumen industry. Due to the development of IPP production processes, the amount of APP produced as a by-product has been declining over time to the point where it is only made on-purpose and no longer as a beneficial by-product. This project aims to create a new avenue of APP production, or at least of a material that mimics APP’s properties so that it can fulfil APP’s applications. Given the large amount of IPP used in short-lived packaging materials, it would be ideal to make such a novel APP using recycled IPP as starting material.
iPP vs aPP
The main difference between IPP and APP is that IPP is semi-crystalline, which is why it has excellent mechanical properties, and APP is completely amorphous, which is why it is somewhat rubbery. To hinder crystallization, defects can be introduced. The random structure of APP offers sufficient defects to prevent crystallization entirely. Considering this difference, it is hypothesized that a significant elimination of crystalline regions should suffice.

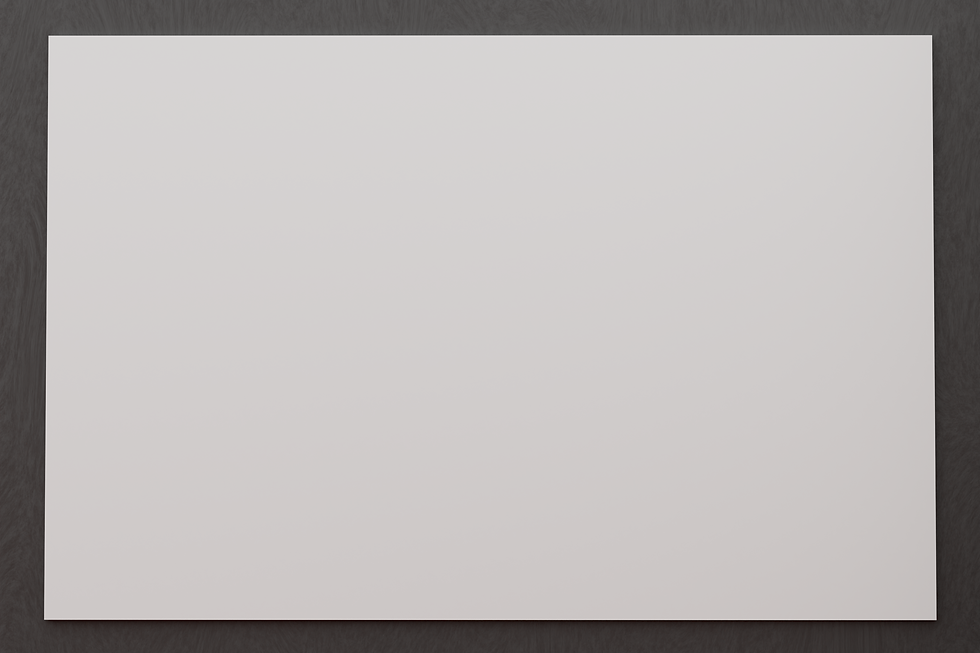
Branching pathways
Besides tacticity, structural defects can also be of a branching nature, where bulky side-groups are introduced to hinder neighbouring chains from coming close. Due to a variety of defects, there are several options to reduce tacticity of IPP. Three theoretical pathways have been constructed with this objective in mind: degradation, branching, epimerization. Let’s discuss these one by one.
Degradation involves a severe reduction in the length of the polymer chains. This can be done is two ways, one using peroxides, in a process called beta-scission [3], and another option is via a thermal pathway, using only heat [4]. The products of both processes contain functional groups that can be exploited for further chemical modification. However, a significant reduction is required to see substantially less crystallization.
Branching works exactly like trees, although trees are hyperbranched. IPP is a linear chain, so to come to a branched product using IPP as starting material is certainly a challenge. It is possible to graft long chains onto the main polymer using either an electron beam process or via reactive extrusion, again involving peroxides [4]. However, a single large chain will not suffice to eliminate crystalline regions from the product. What is needed is something approaching the PP equivalent of linear low-density polyethylene (LLDPE) which has many small branches because it has been made with a mixture of both ethylene and higher alpha-olefins. Since our process relies solely on post-polymerization possibilities, this is not in the scope of this project. Regardless, while branching a polymer, it is always necessary to not overdo it and link all chains together in a process called crosslinking.
Epimerization involves the direct rearrangement of the stereochemistry of IPP. This also involves peroxides, which act as an initiator to abstract an H-atom from the main polymer chain. Using mediators, beta-scission can largely be prevented and chain transfer of H-atoms can be promoted [5]. The only mediator known to do this thus far are bromine compounds. However, due to the highly corrosive nature of such materials, they are not industrially attractive as they would incur high capital cost due to loss of equipment. This project aims to find alternative mediators that can facilitate epimerization.
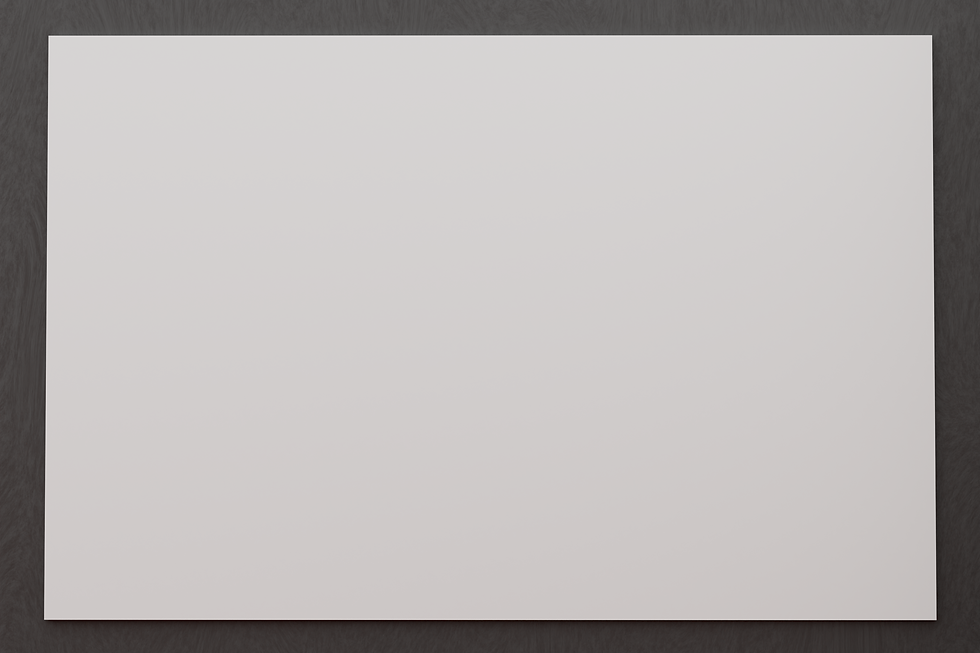
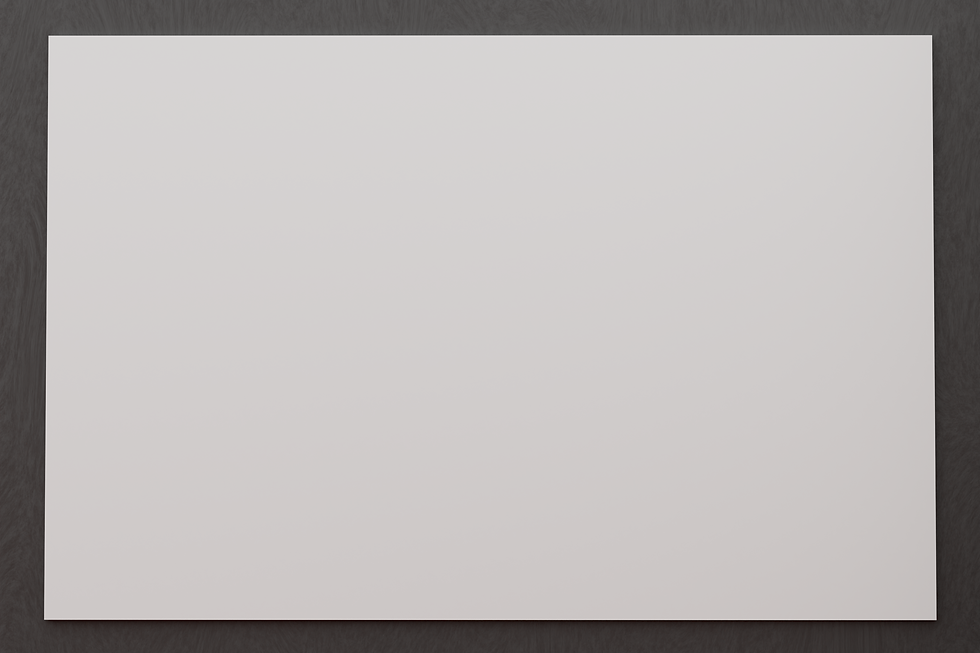
Crystallization
Crystallization is a process that can be either homogeneous or heterogeneous. In case of homogeneous crystallization, the first step is nucleation, which is the first formation of a regular orientation from the melt by the polymer itself. This process is highly temperature dependent, because the newly formed crystalline phase creates a surface tension, and only after a critical size is the crystallization thermodynamically favourable. Just below the melting temperature, Tm, the crystal tends to melt again, so a certain degree of undercooling is required. The lower the temperature, the faster the nucleation process. However, if the temperature is dropped too fast and too low, then the chains will lose mobility required to pack together and the degree of crystallinity will be relatively small, which is known as quenching.
An alternative display of crystallization is the heterogeneous one. In this process, impurities are intentionally added to the melt that offer a surface on which the polymer can grow, effectively skipping the initiation process. Therefore, these impurities are also called nucleating agents (NA). Consequently, this process is usually faster, but the NA do make the process more expensive. However, it should be mentioned that not all NA operate randomly, and their selection is not arbitrary. The surface morphology of these agents must match the morphology of the crystalline polymer, as the growth occurs via epitaxy [1], [2]. As such, the crystal structure is dictated by the nucleating agent. In contrast, there are also NA that dissolve in the melt and form hydrogen bonds upon cooling to create a network of molecules. This type of NA is excellent for transparent materials.
The use of scCO2 is mostly a novelty. A lot remains to be uncovered, but for the time being it is possible to speculate what to expect based on prior research. For example, we know that scCO2 has a plasticising effect, which means the melt viscosity is reduced. This may increase the operating window because lower operating temperatures might now be feasible. It has already been discovered that a lower operating temperature may reduce degradation effects in favour of a modification reaction, such as branching [6].
Given the high diffusivity in scCO2 as compared to that of a polymer melt, the mass transfer of chemical reactants should be much higher, thus speeding up reactions that are not kinetically limited. It should be noted that scCO2 merely facilitates mass transfer, whether that concerns an insertion or an extraction of chemicals depends on the concentration gradient. As such, care should be taken in its application, as scCO2 may extract additives while processing a polymer. This can be extremely useful for recycling processes, but if the additives are added to improve certain functionalities, they should not be removed while processing the material.
scCO2 as processing aid
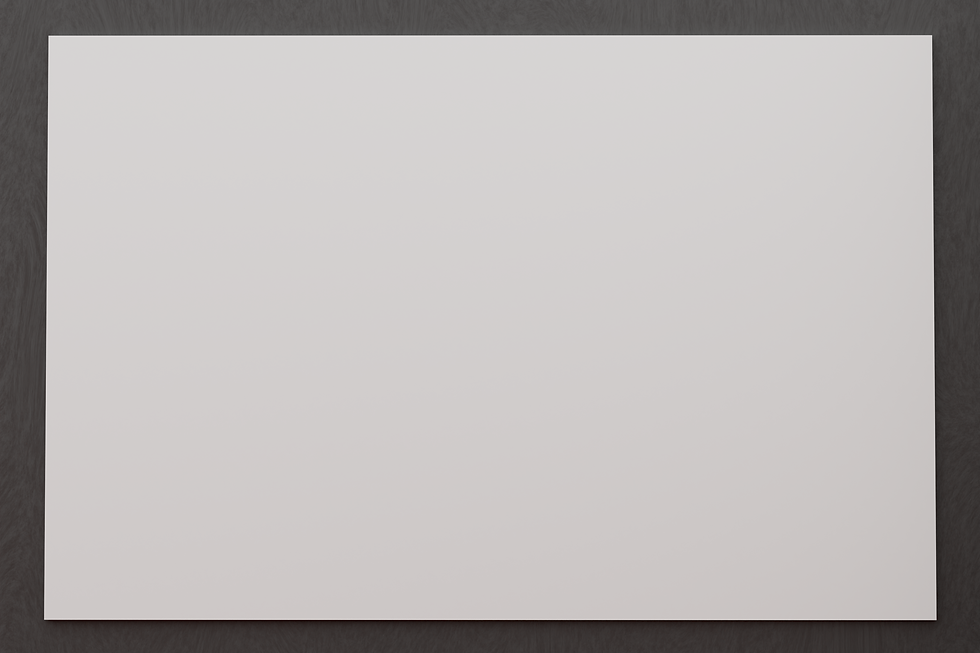
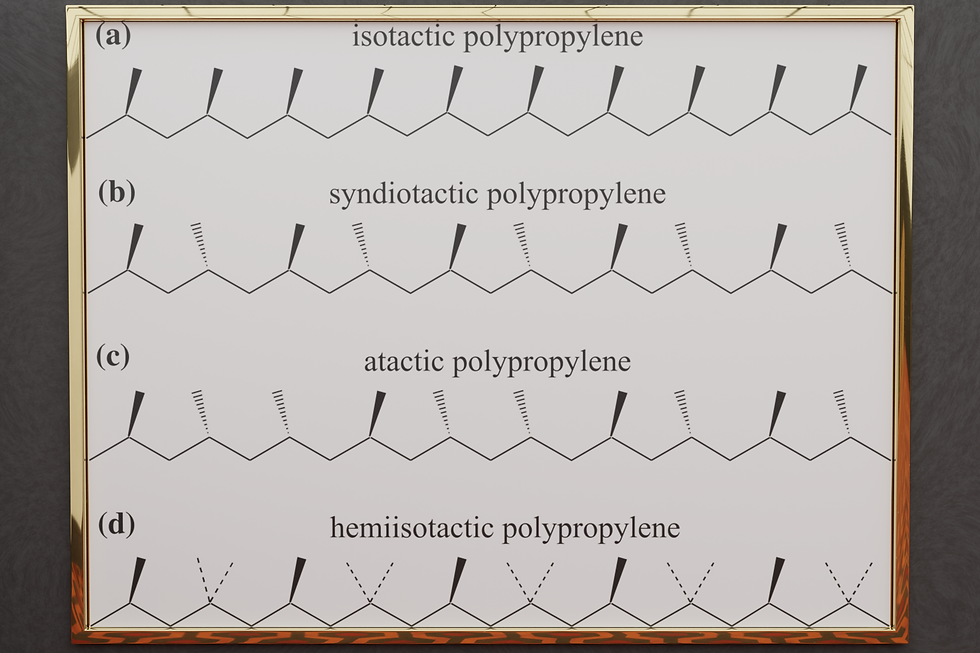
Tacticity is a phenomenon that arises during polymerization. Propylene is a very simple molecule, with just 3 carbon atoms, and 6 hydrogens. Two of the carbons are linked with a double bond instead of just a single one. These double bonds are what allow the individual molecules to link up, and when they link into a linear chain, we call that a polymer.
However, that means that only two of the three carbon atoms of each propylene molecule end up in the chain, and so every second carbon along the chain has another carbon sticking out to account for that third carbon in the propylene molecule. That third carbon can either stick out to the left of the chain, or to the right. It's a binary option. For a single unit, it doesn't really matter where the third carbon goes, but for the entire chain as a whole, it matters what each individual propylene unit does. This is where a new phenomenon comes into play: tacticity.
In a way, each polypropylene chain exhibits a certain binary sequence, and as with some sequences, one is able to recognize a pattern. Such is the case with tacticity as well, and so we distinguish a small variety of different types of tacticity based on the pattern that the chains display.
-
Isotactic, where all the carbons stick out in the same direction.
-
Syndiotactic, where all the carbons stick out alternatingly, yet in a regular sequence.
-
Atactic, where all the carbons stick out in a totally random way.
-
Hemiisotactic, which is a random combination of the first two.
These are the relevant types of tacticity, as these are the variations that we have the technology for to produce them. It would not be hard to call out other regular sequences such as the famous Fibonacci sequence, but that sequence is too complex to manufacture, and so that type doesn't have a name.
The variations of tacticity

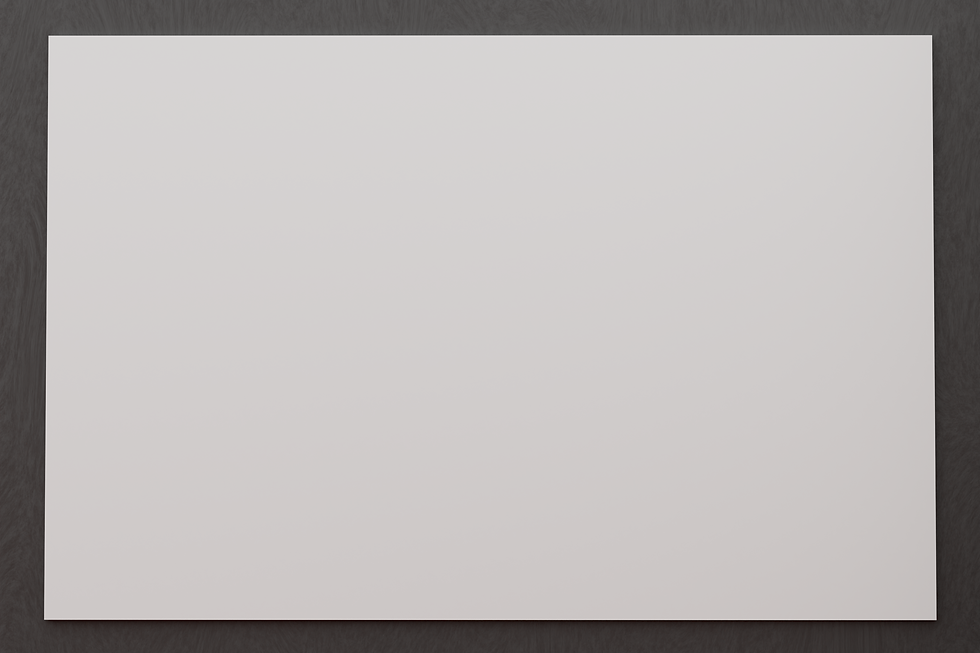
References
[1] J. C. Wittmann, A. M. Hodge, and B. Lotz, “Epitaxial Crystallization of Polymers Onto Benzoic Acid: Polyethylene and Paraffins, Aliphatic Polyesters, and Polyamides.,” J. Polym. Sci. Part A-2, Polym. Phys., vol. 21, no. 12, pp. 2495–2509, Dec. 1983.
[2] B. Lotz, S. Graff, and J. C. Wittmann, “Crystal morphology of the γ (triclinic) phase of isotactic polypropylene and its relation to the α phase,” J. Polym. Sci. Part B Polym. Phys., vol. 24, no. 9, pp. 2017–2032, Sep. 1986.
[3] C. Tzoganakis, A. E. Hamielec, Y. Tang, and J. Vlachopoulos, “Controlled degradation of polypropylene: A comprehensive experimental and theoretical investigation,” Polym. Plast. Technol. Eng., vol. 28, no. 3, pp. 319–350, 1989.
[4] T. Sawaguchi, T. Ikemura, and M. Seno, “Preparation of α,ω-Diisopropenyloligopropylene by Thermal Degradation of Isotactic Polypropylene,” Macromolecules, vol. 28, no. 24, pp. 7973–7978, Nov. 1995.
[5] G. R. P. Henry et al., “Controlled reduction of polypropylene lsotacticity and crystallinity by epimerization during reactive processing,” J. Polym. Sci. Part A Polym. Chem., vol. 47, no. 18, pp. 4505–4518, Sep. 2009.
[6] M. Rätzsch, H. Bucka, A. Hesse, and N. Reichelt, “MODIFIED POLYPROPYLENES OF IMPROVED PROCESSABILITY,” EP0879830B1, 1997.