

The Preservation of Flowers
Preserved flowers could immortalize important botanical findings and personal events in life, such as graduations, weddings and anniversaries. Their minimal required maintenance would facilitate their use as semi-permanent decoration for offices, store windows and retirement homes and besides that, broaden their geographical market to regions where the fresh equivalent is not able to thrive. It could also save in logistic costs as quick and refrigerated transport would not be required, enabling the options for slower, cheaper transport.

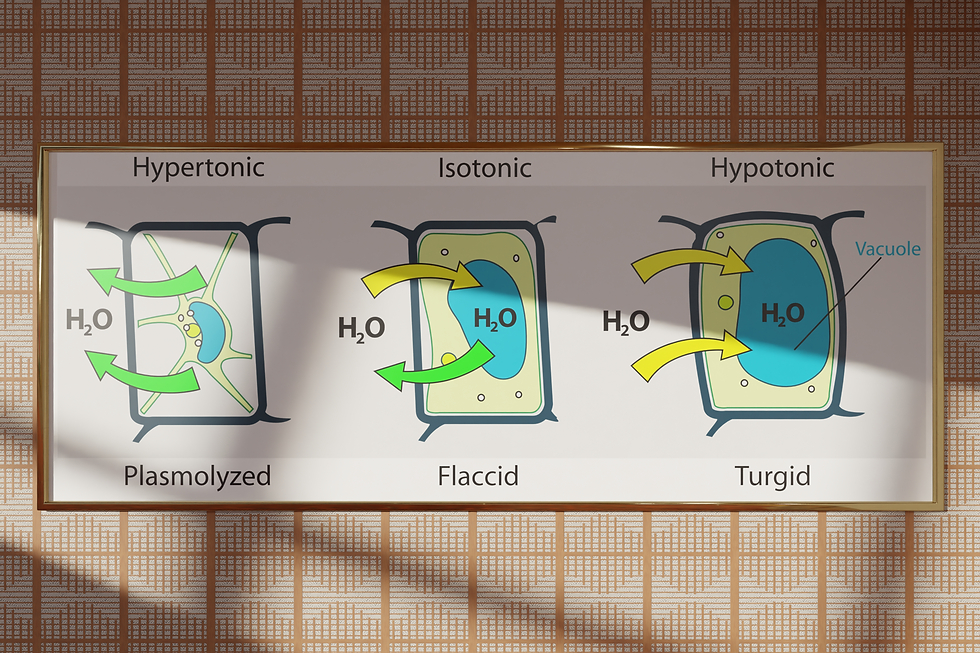
The structure and rigidity of fresh flowers is provided by the turgor pressure. This hydrostatic pressure is maintained as long as the concentration of minerals inside a cell is higher than the concentration of minerals outside of it. There are two ways in which minerals can naturally flow inside the cells of living flowers. One is by absorption of minerals from the soil and from water, whereas the other is by synthesis of sugars inside the cells. Both of these actions however, cost the flower energy, thus creating a difference in potential inside- and outside of the cell. Water will diffuse from regions with high energy to regions with low energy and thus water will flow inside the cell during this hypotonic state in the process named endosmosis. The accumulation of water inside the cell causes the cell membrane to swell, pushing against the cell wall. This effect provides the turgor pressure responsible for the structure and rigidity to the flower [1].
When the stem is cut or the flower is separated from its roots otherwise, the supply of minerals is cut short. This switches the system from a hypotonic state to the hypertonic state. As a results of plasmolysis, water starts leaking out of the cells, eventually causing drying, wilting and shrinkage of the flower.
Turgor Pressure


Current preservation procedures
The general concept to preserve biological material revolves around the inactivation of water. This can either be achieved by physical removal of water from the plant tissue, or by incorporating compounds that bind to water. Over the years many concoctions and procedures have been proposed to maintain the texture and flexibility of their fresh counterparts, where every ingredient has its specific function in dehydrating, bleaching, plasticizing and colouring the flowers. Common side-effects however, are shrinkage, a brittle product and loss or change of colour and colour intensity [3]. More importantly, the procedures often consist of lengthy processes utilizing costly, potentially hazardous, organic solvents.
Longbloom, the industrial sponsor of this project, currently utilizes the alcohol procedure to preserve (mainly peony) roses. This process consists of a three-step procedure, comprising of [4,5]:
-
Multiple submersion cycles in a dehydrating agent;
-
Single submersion cycle in an impregnating agent;
-
Drying and removing excess material using supercritical carbon dioxide.


The alcohol procedure does, however, use a large quantity of solvent and despite that the procedure is generally quicker than traditional processes, it still takes several days to process flowers. Besides that, the biomass is impregnated with fossil-based compounds, which adversely affects bio-degradability. Still, using this method, the processed flowers can maintain their natural properties (figure 2), where most importantly shrinkage does not occur, in contrast with air drying.
Air drying results in shrinkage as a result of capillary forces, which collapse the pores and destroy the structure of the flower. Supercritical carbon dioxide (scCO2) has high diffusivity and no surface tension, thus can extract compounds from the substrate without collapsing the pores. CO2 in particular has many interesting (green) properties as well, such as being non-toxic, non-flammable, inert, apolar, mild supercritical conditions, and having low costs. Therefore, Longbloom uses scCO2 in the final step to dry the processed roses.
Despite that the traditional alcohol procedure works well, the large quantity of solvent, lengthy processing time and biodegradability are the main points that require addressing. Therefore, the main question is whether the process can be simplified into a single-step process by removing or integrating pre- and post-treatment steps, while maintaining the natural properties and ideally while making the process and products ‘green’. To simplify the process, the multi-step procedure has been translated into a stirred batch reactor (below left). The reactor is supplied with scCO2, is temperature controlled (automatic), pressure controlled (manually) and supports injection and removal of solvents. The programmes consist of (multiple) dehydration cycles, followed by rinsing steps and impregnation cycles.
To improve reproducibility and potential scale-up, the reactor has been modified to introduce a continuous scCO2 flow, allowing the system to operate semi-continuously (below right). A proof of principle has been executed which shows that similar results can be obtained compared to the batch procedure, while further reducing the quantity of solvents used and while further reducing the process time from three – four hours to one – two hours.
Supercritical CO2 as intensifying agent


This batch procedure gives good results for white African roses and decent results for Naomi Red roses. A common obstacle is disintegration of the 'harder' parts, like the sepals, stem and receptacle during the depressurization phase. This likely occurs when the system contains too much water after processing where rapid expansion of CO2 violently escapes brittle material, causing it to explode. Overall, the process time is reduced from several days (traditional alcohol procedure) to merely three – four hours in the batch reactor. The batch reactor requires quite some micro-management however, which affects reproducibility and thus at this moment makes it unsuitable for scale-up to industrial levels.
The processed roses, both for the ones processed in the batch- and the semi-continuous reactor, have a non-uniform colour and still require quite a bit of organic solvents. The aim is to reduce the quantity of solvents and plasticizers as much as possible, while optimizing the product properties by bleaching and dyeing during the process inside the reactor.
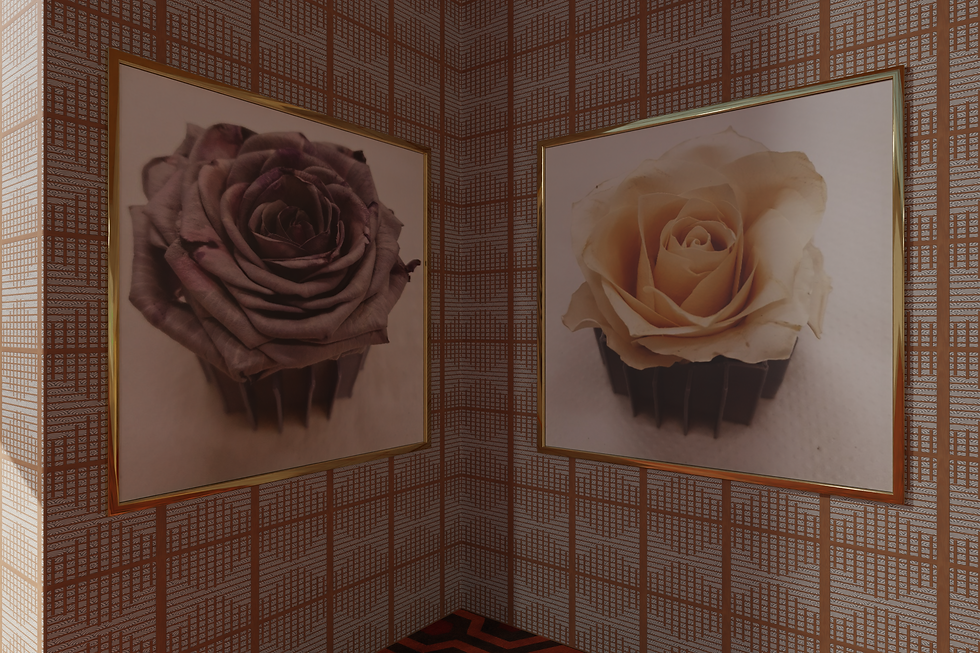
Initial Results


[1] Fricke, W. (2017); Turgor pressure Encyclopedia of Life Sciences; ISBN: 9780470015902
[2] Wikimedia Commons (2020); Turgor pressure on plant cells diagram
[3] Zeelie, B. et al. (2014); US 8819990 B2: Preservation of Plant Material
[4] Longbloom IP B.V. (2014); WO 2014/189376: A method of preserving fresh ornamental plant parts
[5] Longbloom IP B.V. (2014); WO 2014/189377: A method of reinforcing fresh ornamental plant parts
[6] Goodship, V.; Ogur, E.O.; (2004); Polymer Processing With Supercritical Fluids ISBN:1-85957-494-7
[7] Wikimedia Commons (2010); Phase diagram of CO2